Mobile Crane Maintenance & Brake Testing
Crane maintenance
DVSA mobile cranes HGVs
DVSA’s push a few years ago to bring mobile cranes into the annual test requirements also faced by HGVs have been supported and aided by the CEO of the country’s largest crane rental firm by units, Ainscough Crane Hire, writes Will Dalrymple
Chief executive officer of Ainscough Crane Hire, Peter Gibbs, also heads up the Crane Interest Group at trade group the Construction Plant-Hire Association, and it was through that organisation that he worked first to develop an annual testing standard document at the time, and then last year adapting the Guide to Vehicle Roadworthiness and HGV inspection manual for the use of group members (see www.is.gd/bayuho).
Mobile cranes divide into two types: those built on top of a bespoke chassis and those on a standard HGV base, also known as ‘truck-mounted’ cranes. Usually the former are, as engineering plant, exempt from the normal Construction & Use and Authorised Weight rules of the road; in particular, they tend to have much higher axle weights (up to 16.5t) and potentially many rows of axles. The usual crane derogation is known as STGO (standard type general order): its categories 2 and 3, among other precautions, limit motorway speeds to 40mph.
But Gibbs doesn’t just want to help the crane industry comply with the new rules. In fact, the documents are part of a bigger mission. He says: “These are stepping stones toward a position where I, and the membership, would like to see that dispensation removed, and see that governance for HGVs applied across mobile cranes.”
“They can sit on site, but they typically travel between once and five times, depending on the job. I think it’s an anomaly that they have not been subjected to [HGV] compliance standards all along.”
Asked to elaborate, the executive, who is a 2022 winner of the Sir Moir Lockhead safety award (see
www.is.gd/julune) continues: “It’s fundamentally about safety. The history of the sector in the last 20-30 years has been a combination of cheap money, the ability to lease a crane at very little cost, made it easy, as well as equipment that is sat outside of standard regulations. This has created a two-tier operating model.
“The downside of that, and this is evidenced, and it still happens in some places, is that some operators will not and do not maintain the crane to the safe, roadworthy standard.
“The probability of something going wrong with a crane is low, but its impact is high, on the highway travelling and on a customer’s site. For that reason as well, we want to know that the industry is putting out a well-maintained, roadworthy and lift-worthy piece of equipment with a properly briefed and trained operator with the right competency to carry out the job, both in getting from A to B and in carrying out the lift. Because when it goes wrong, that doesn’t make a pretty picture.”
The practice of maintaining roadworthiness is also relevant for a mobile crane business because, even if the mobile cranes are able to travel under their own steam (or in Ainscough’s case, HVO – see below), most crane hire firms will still need an O licence anyway to transport their counterweight, tackle and accessories.
Alongside its 400 mobile cranes, Ainscough operates 30 HGVs, all of which are now compliant with Transport for London’s Direct Vision progressive safe system, he says. And, in a claimed first for the UK crane hire industry, it has also become an Earned Recognition operator, the audit for which also saw its mobile crane fleet audited.
STGO classification also exempts cranes from the braking performance requirements of normal HGVs. (Minimum in-service brake performance for a crane running under STGO Cat 2 is 62.5m at 40mph with braking efficiency of 30%, for example.) Also, because of their size and weight, many cannot fit into authorised test facilities for a periodic roller brake test, so instead decelerometers are still commonly used.
Gibbs justifies that reporting procedure by saying: “Decelerometers don’t necessarily give the same results on every axle as a brake tester would, but they give good evidence that the crane can stop within the constraints. These are practical solutions of what we can do, and [provide] reasonably good assurance in this case that the equipment is safe – if you combine that with evidence of routine maintenance – and that the brakes have had visual inspection and testing.”
The requirements do allow a third option, a measured stopping test, but Gibbs reports that Ainscough does not use it.
In other ways, though, Ainscough treats cranes just like HGVs. The majority of them are put on a six-weekly inspection cycle (eight weeks if new). Ainscough has implemented daily walk-around checks for cranes and HGVs, and in fact has developed several tools to aid this process. One is a recording process for checks using a digital device similar to a mobile phone that populates online records with information and photos. A second is sticking QR codes on to the cranes, which the person carrying out checks must scan as he or she works their way through the inspection process. HGVs are geofenced so the company can ensure pre-start checks have been done before drivers head off, and during their journey their behaviour is also monitored. That technology is also coming to the crane fleet as well.
Adds Gibbs: “We can see both in terms of periodic and by mileage maintenance when a crane is due, and make sure we schedule it in. We can and do extend the maintenance schedule if the crane is sited somewhere, and we have an interim inspection process that we adopt in that case.” If the customer agrees, the company will even swap out cranes working on a jobsite, if a periodic inspection is due.
A key part of the company’s current strategy revolves around its 30 nationwide depots and 28 workshops where it carries out its own maintenance (and trains up the fitters in its own Level 2 and Level 3 plant maintenance apprenticeship, delivered in Preston with Myerscough College). “Our engineers work above and below the deck [of the crane] in the same scheduled maintenance programme,” as Gibbs puts it.
REGIONAL APPROACH
Depots became much more important in the business some four years ago, when Ainscough began to regionalise the business to provide a local offering. The MD explains: “It is the most efficient and environmentally friendly solution. Rather than a profit centre in the south sending a crane to Scotland because it won a job, that job is picked up and dealt with by the local team in Scotland. The benefit is local service, fewer miles and less backup.” He reports that the change has reduced mobile crane mileage by a third, overall.
It is also upgrading the crane fleet to single-engined models (older units have a second diesel on the superstructure) fitted with Stage V engines, the non-road mobile machinery equivalent to Euro VI. That, plus the switch from diesel to HVO, as well as setting up TPMS on all cranes, optimising the rigging tackle box they all carry and buying a small quantity of offsets, have together enabled the company to be certified carbon neutral in operation.
All of these operational improvements are linked, and together provide a number of benefits, Gibbs concludes: “In terms of the environmental piece, good safety is good service is good cost performance.”
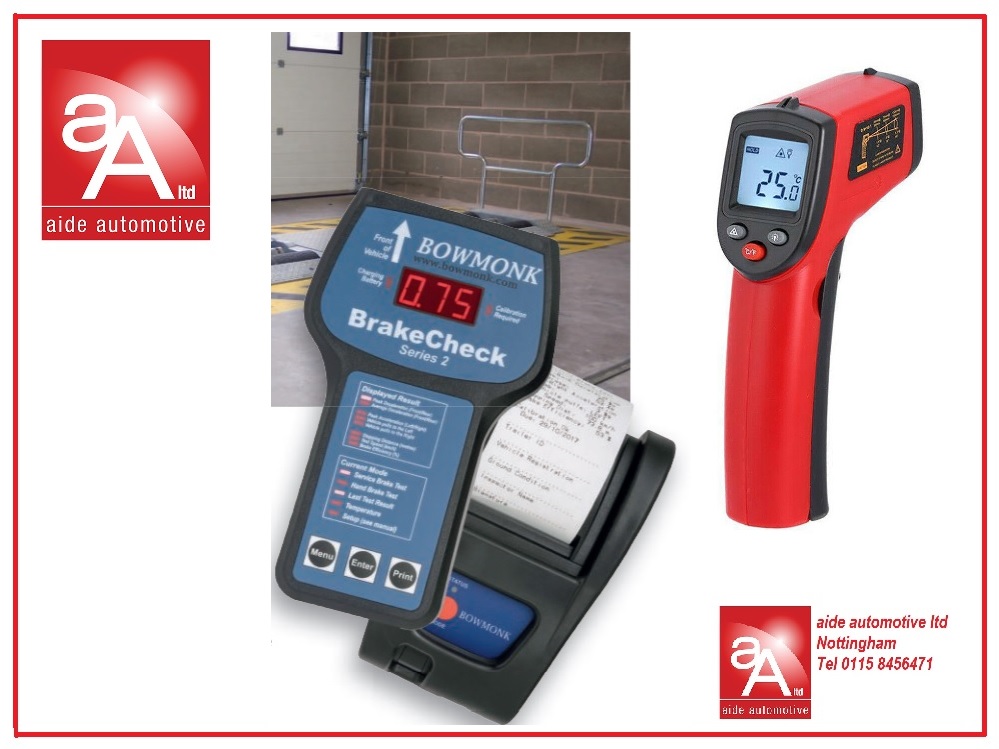